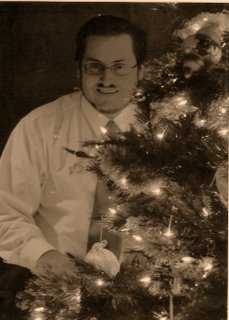
Hello to all!
Let me take this opportunity to wish everyone a Merry Christmas!
It has been quite the year here at Ulm Orgelwerke and I have this distinct sense that the upcoming will be just as interesting. Only time will tell.
As the new owner, I will be changing many things. However, the things that have made this company a success will not change: the drive for quality, ethical business practices, and an openness to change will all still be a part of UO under the second generation of ownership.
New procedures, new attitudes, new avenues to explore-all of these will make UO the "builder of choice" now and into the future.
Thank you to all of our customers and suppliers. Best wishes for a prosperous new year.
Drew E. Meyer